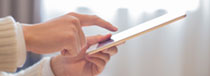
手機:18011319033(微信同步)
郵箱:258046925qq.com
地址:四川省成都市武侯區武科西
一路85號鼎晟國際B棟一單元
1 緒論
國內錳、黃金浸出、鋰鹽等稀貴金屬選礦冶煉過程中為提高貴液中有價金屬回收等領域,需要對物料進行多次過濾洗滌。國內企業常規都是采用脫水、洗滌作業分段進行,由于洗滌與過濾分別在不同設備中進行,且在洗滌過濾循環過程中物料需要重新配漿,存在工藝流程繁冗,設備種類多,除了導致企業生產運行成本高,更存在物料廢渣中有害金屬超標,堆存排放安全隱患大,增加環保壓力等一系列問題。
近年來,國家對各行各業的環境保護和資源利用要求越來越高,大力提倡節能減排、清潔生產、綠色制造。針對上述行業的脫水工藝流程及過濾洗滌現狀,國內相關領域的技術專家在脫水、洗滌工藝及設備上做了大量的優化改良工作,但基本上都是單一流程的優化,缺乏把兩者高效結合起來研發成果,現今,我們研發并推廣一種新型的短路節能、過濾洗滌一體技術及相關處理配套設施,滿足最終濾渣產品的洗滌率及含水率能達企業希望的既定指標,解決廢渣達標,同時縮短傳統濃密洗滌過濾工藝流程,降低投資運行成本,該技術的成功研發對企業是有著良好的使用價值及在相關領域的推廣前景[1-5]。
2 新型過濾洗滌一體技術在電解錳廢渣脫水洗滌的試驗研究
2.1 新型過濾洗滌一體技術現場試驗目的及意義
四川某錳礦屬大型民營電解錳生產加工企業,錳電解主要采用為酸浸電解工藝,現場工藝處理過程中除了生產出電解錳產品之外,還會有大量碳酸錳渣粉(每生產1頓電解金屬錳會同時產生5-6噸錳廢渣)附帶產出,由于錳礦渣產出量大,其中又含有大量硫酸鹽、氨氮、砷、汞、鎘、錳等重金屬離子物質,屬于有害廢渣,長期堆放不但污染當地環境,也是對有價金屬錳的嚴重浪費。現場脫水工藝是對浸出錳渣液采用采用濃密、壓濾兩段工藝流程進行過濾洗滌處理,即礦漿首先進行濃縮,隨后碳酸錳礦粉浸出液通過傳統的板框式壓濾機進行濾液粗壓,進而在加藥劑沉淀進行第二次甚至是多次壓濾、最終產出電解金屬錳渣產品的方案。由于該工藝流程中采用傳統壓濾設施(普通板框壓濾機)進行的兩次(或者多次)脫水作業,流程中碳酸錳礦粉的由于缺少洗滌流程,導致處理后的電解錳渣中硫酸銨、硫酸錳含量偏高。企業技術人員為了解決實際存在的問題,也嘗試采用了壓濾后的錳渣用清水洗滌后再壓濾的方案,但是洗滌率效果不佳,洗滌率指標化驗都在60%以下,不但二價錳流失嚴重,工藝流程還繁瑣,也加重了設備負荷。此外,脫水主要工藝指標含水率也在22%左右的一個偏高指標,均都無法達到一個符合要求的工藝指標,不但造成有價金屬浪費,也給企業造成了運營成本的增高及經濟效益的降低,此外,環保污染問題也無法從根本上得以解決。
現階段,在現場進行高效過濾洗滌設備的技術研發及試驗研究,通過新技術的更新,推出一種既能充分完成洗滌作業,高效浸出液錳渣中的有害金屬離子,在完成同等或更優濾餅含水率及洗滌指標的條件下,錳渣能符合環保標準作為副產品產出,并能在現場有效實施的工藝方案。進而實現洗滌、過濾工藝無短路一體化,大幅縮短工藝流程,減少有害物質的二次污染,提升有價資源的回收率,降低企業投資及運行成本,提升企業的經濟及社會效益[6-7]。
2.2 試驗要求及目標
針對現場實際情況,本試驗主要是采用具有壓濾、脫水一體化工藝及配套設施替代傳統設備進行脫水洗滌流程的半工業試驗,通過對碳酸錳礦粉浸出液進行洗滌和脫水處理,將原工藝繁瑣的多次處理流程通過一臺設備一次處理完成,力爭最大限度回收錳渣中硫酸錳、硫酸銨等有用物質,錳、氨回收率目標預計達到98%以上(濾液Mn2+>25g/l,廢渣Mn2+<3g/l),實現錳渣無害化。最終驗證該技術設施在實際生產的應用效果,為企業提供一種具有新型高效節能環保技術的工藝及其配套設備。
試驗還將對處理后的物料進行檢測,對最終錳渣產品二價錳含量及其洗滌率指標進行分析,與原有工藝的二價錳的洗滌率相對比,從而得到現場實際的數據,作為新型一體化工藝的理論數據,從而判斷新型壓濾洗滌一體化技術及設備的應用處理效果,為企業降本增效提供更優的技術升級方案和工藝設備支持,實現企業的資源化利用和達到環保要求,真正提高企業經濟效益。
2.3 試驗物料及試驗設備參數簡介
本次試驗主要工是工藝流程技術及其設備性能的研究,因此沒有相關的藥劑及流程選別試驗。
試驗樣品為壓濾車間內的實際生產的電解錳渣物料,由現場負責采集。礦漿溫度 32-38°C;
干礦比重3.04;物料濃度18%;礦物主要組成見表1:
表1 主要礦物的化學組成
試驗采用的設備是CJWA-5/4/30型高能壓濾機的工業實驗模擬機。該機型自身即具備高效過濾性能,并根據本次試驗得技術要求,在設備整體結構上做了技術升級,使其兼備高效洗滌和過濾功能,從而能滿足工藝試驗技術要求。
主要試驗設施參數:濾板過濾面尺寸500×500;濾餅數量4塊;濾室深度30mm;采用渣漿泵給料;壓榨、吹干介質共用為壓縮空氣;攪拌槽規格φ800×1200;儲氣罐容積2m3;洗滌水為生產用清水(采用電加熱器加熱至所需溫度)。
2.4 試驗主要方案及步驟
本次工藝試驗研究,主要是進行碳酸錳礦粉浸出液的產品脫水試驗,試驗將進行新技術的多級洗滌工藝試驗、洗滌效率指標對比試驗,通過洗滌率的參數對比確定工藝指標,檢驗新設備使用效果及性能參數,最終提出合理可靠的脫水洗滌工藝和設備數據指標,并判定新型一體化洗滌技術及其相關設備的性能。
a. 多級洗滌試驗
用具備新技術的設備對現場浸出液進行常規壓濾及洗滌壓濾,并根據壓濾濾液出水情況及渣漿泵壓力情況對給料時間、壓榨風干時間,洗滌時間等參數進行設定和調整。試驗主要是在設備內部對濾餅進行多次洗滌、循環,直到整個系統達到平衡。
試驗原料取自現場礦漿高位礦漿桶,原漿溫度在30-38℃左右,為保證較高的洗滌效率,進料時間首次設定35分鐘,進料原則是沒有壓濾水排出,濾餅厚度約3cm。試驗一級洗滌水用水量約45L,當洗滌水中Mn2+>25g/l時,即可達到試驗要求。試驗首先加入15L的清水進行第一次洗滌,洗滌液收集后再加入15L清水進行第二次洗滌、第三次洗滌,洗滌液循環使用,直至到達試驗數據的要求。一級洗滌結束后在進行二級洗滌試驗,程序和第一級試驗步驟一樣。每一級洗滌時間在20分鐘左右,把45L的水洗完。從第一組試驗Mn2+的數值達到要求后,再在每一組試驗之后用15L的自來水洗滌,再洗滌三次Mn2+的數值又可達到試驗要求,這樣保證試驗過程中加入的水和出來的水達到水平衡,從而達到污水零排放的要求。其中,洗滌效率試驗是本次試驗成功的關鍵,用洗滌水將原漿中的游離錳和硫酸銨洗出98%,能實現錳渣無害化處理。試驗中主要需要控制的參數包括進料時間、新加水量、洗滌時間、洗滌效率。
本次試驗將對每一組洗滌水(按水溫35℃左右)和直接壓濾水進行取樣分析,檢測最終物料的Mn2+、硫酸銨、水分、全錳。
試驗流程圖見圖1;數據分析見圖 2;圖3所示。根據圖中數據可知,一級水在經過9次洗滌后Mn2+的值為29.13g/l達到試驗要求(Mn2+的值>28g/l),二級水在10次洗滌后Mn2+的值為29.25g/l后達到試驗要求(Mn2+的值>28g/l)。
b. 滌效率試驗
碳酸錳礦粉浸出液通過泵將浸出液從壓濾攪拌槽泵入實驗機攪拌槽進行過濾及洗滌流程試驗。最后采用高錳酸鉀滴定法測定濾液及洗滌液中二價錳含量。通過測定浸出液和經過過濾洗滌之后的洗滌液中二價錳的含量,計算新工藝條件下的洗滌率,進而對原有工藝條件下的洗滌率進行對比,以此判定新工藝流程的洗滌質量。
原有脫水工藝和新脫水、洗滌工藝在壓濾、洗滌質量上不僅存在差別,在單位浸出液的處理能力上也存在差別,試驗通過對同樣數量的浸出液進行處理,以處理后的濾餅的密度作為共同目標,通過測定新工藝的用電量和功耗,進而對新舊兩種工藝的處理能力進行對比。
3 試驗結果分析及結論
本次試驗是對過濾的礦樣進行試驗,并對每一組洗滌水和直接壓濾水進行取樣分析,試驗的目標是將濾餅密度過濾至統一的密度,在達到這同一標準的情況下,檢測設備在各個過程中需要的參數和時間,通過過濾、洗滌工藝和之前只有過濾工藝的流程進行對比,進而得到兩個工藝流程的工藝參數差別。其次,對兩個流程的處理效率進行對比,測定壓濾液和尾渣中的二價錳的含量,通過壓濾液和尾渣中的二價錳的含量的對比,計算洗滌率。試驗數據及試驗工藝參數見表2。
表2 壓濾洗滌試驗數據分析表
通過試驗結果表中看出:新工藝其洗滌效果比較穩定,平均洗滌率高達94.44%;根據圖表數據可知,在經過洗滌后,濾液中Mn2+的值為25.12g/l~29.12g/l,本次試驗已完成了既定的目標要求。通過試驗結果分析,得出了以下結論:
a. 通過對濾洗滌參數及最終二價錳的化驗分析結果,可以看出該浸出液屬于易過濾易洗滌物料,通過實施新工藝路線洗滌率能到到符合要求的高指標,也精簡了工藝流程,降低了能耗指標。
b. 根據洗滌前濾餅中二價錳含量等于壓濾濾液中二價錳含量,我們按此進行洗滌率計算,試驗的洗滌率平均值為94.22%(按洗滌水量為0.7-0.85倍濾餅重量)。在工業生產中,洗滌率可以保證在90%以上。
c. 根據試驗數據可知,經過洗滌后的溶液游離錳含量能達到25g/l以上,可滿足現場試驗要求,因此,工藝流程及洗滌、過濾設備下一步將可用于生產。
d. 新工藝充分利用了物料性質,新設備由于采用了全自動控制系統,并應用了新介質和特殊設計結構構的濾板,在內部又注入了和高壓空氣,使其造兼備高效、節能的壓濾技術,既能將碳酸錳礦粉中的二價錳充分洗滌出來,更提高了脫水率指標,新工藝流程最終錳渣含水在16%左右比原工藝指標提高了6個百分點,可大大節約尾渣下一步的對外運輸成本。
4 小結
綜上可知,本次試驗采用的新工藝及其相關設施,在原有同等生產條件下,將壓濾、洗滌流程進行了一體化集成,取代了兩段或多段聯合洗滌脫水工藝,使得脫水流程更加精簡、效率更高、設備臺數更少。經過對比原工藝和新工藝兩種情況下的壓濾洗滌效果,可以看出,新工藝不但工藝環節少、自動化水平高,在主要技術指標平均洗滌率和脫水率上,比原工藝條件下的生產實際平均指標均有大幅度提升,洗滌效率這一關鍵指標數據的提高說明新工藝試驗效果良好。此外,通過原工藝流程和壓濾洗滌一體化工藝的對比,在設備成本增加不多的情況下,壓濾洗滌工藝能回收更多的錳,并降低廢渣錳含量,并能將之前無法排放、利用的廢渣變成可利用能外排的有用物質,提升了有價資源的回收,產生的社會、經濟效益利益極為明顯。
1.蘭州有色冶金設計院有限公司 ; 2. 成都長杰科技有限公司
主要作者簡介:劉誼兵(1969-),男,上海市人 ,高級工程師, 主要從事有色、黑色礦山設計、咨詢及相關領域的技術研究
參 考 文 獻
[1] 選礦設計手冊編委會 選礦設計手冊,冶金工業出版社1988
[2] 杜兵等,電解錳渣處理處置技術及資源化研究進展與展望 [桂林理工大學學報]-第35卷第1期2015年2月
[3]楊德武,王達理.鉻黃濾餅洗滌吹干效果的實驗研究 [期刊論文]-過濾與分離2011(4):4-7
[4]都麗紅,王士勇,鄧伯虎,朱企新. 濾餅過濾中濾餅的洗滌及應用[期刊論文]-化學工程2011(8):40-43
[5]熊筱. 對電解錳進行清潔生產效果及其指標體系可行性分析,貴州大學學報 -第26卷第1期 2009.2
[6]姚公弼.固液分離的應用和發展概況【J】.過濾與分離1994(2):1-8
[7]趙博超,王雪婷等. 洗滌方式對電解錳渣中錳回收效率及無害化處理的影響 [期刊論文]-《環境工程學報》,2017(11)